
What is wrench time and how can you improve it
Ciprian Chiripuci
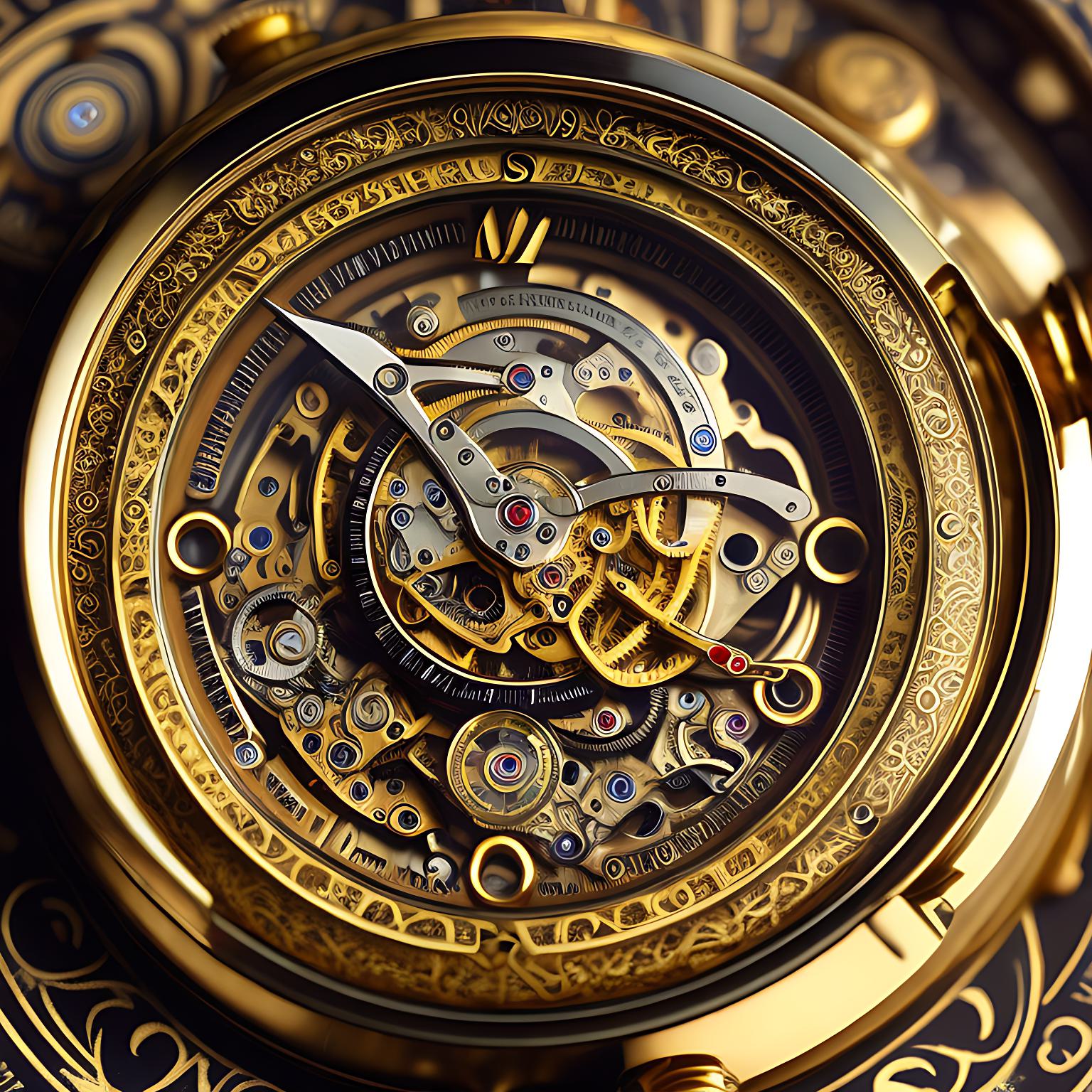
Through searching infos about CMMS, asset management or preventive maintenance, for sure you encountered often this expression: wrench time.
But, what is wrench time?
Wrench time refers to the actual amount of time that maintenance technicians or mechanics spend working on equipment or performing maintenance tasks, as opposed to time spent on non-value-added activities such as searching for tools or waiting for materials.
Why is it important?
Improving wrench time can help organizations reduce maintenance costs, increase equipment uptime, and improve overall maintenance productivity. By increasing the amount of time that technicians spend working on equipment, organizations can minimize downtime and improve equipment reliability. Improving wrench time can have a significant impact on maintenance productivity and cost-effectiveness.
So, how can organizations improve wrench time?
There are lots of ways that organizations can improve wrench time, including:
Providing well-organized workspaces: A well-organized workspace can help technicians find tools and materials they need quickly, reducing the amount of time spent searching.
Standardizing work processes: Standardized work processes can help reduce the time required for maintenance tasks by eliminating unnecessary steps and ensuring that technicians have the tools and materials they need before starting work.
Implementing a computerized maintenance management system (CMMS): A CMMS can help organizations track maintenance activities, schedule preventative maintenance, and provide real-time data on equipment performance, all of which can help reduce downtime and improve wrench time.
Providing training and development opportunities: Training and development opportunities can help technicians improve their skills and knowledge, allowing them to work more efficiently and effectively.
How can you measure wrench time?
Track the time spent on maintenance activities: Organizations can track the amount of time that technicians spend on maintenance activities, and compare it to the amount of time spent on non-value-added activities such as waiting for materials or searching for tools.
Track equipment downtime: Organizations can track equipment downtime, and use this data to identify areas where wrench time could be improved.
Conduct time and motion studies: Time and motion studies can help organizations identify areas where maintenance tasks could be completed more efficiently.
So, as you can see, wrench time is an important KPI for organizations that rely on maintenance technicians or mechanics to keep their equipment running smoothly. By adopting best practices, such as providing well-organized workspaces, standardizing work processes, implement CMMS and CWMS, organizations can improve wrench time, reduce maintenance costs and improve equipment uptime.
Related posts
Here are some resources to help you get more out of your assets

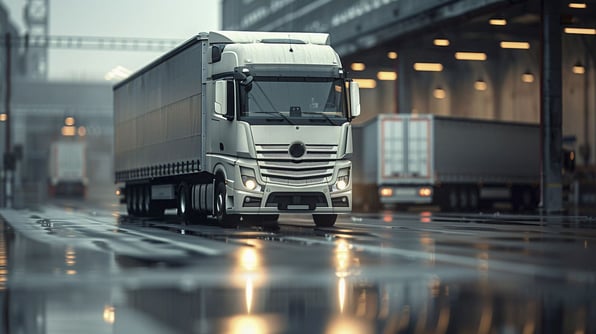
Ciprian Chiripuci
Truck Sealing in Delivery Logistics: Definition, Benefits and Best Practices
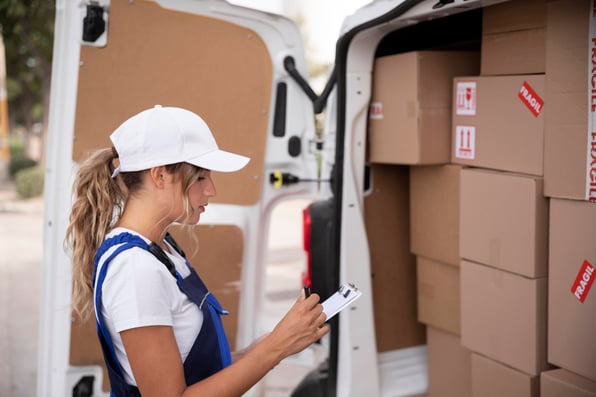
Ciprian Chiripuci
Mastering that Last Mile
READY TO TALK?