
Top 10 Reasons for Equipment Failure: Avoiding Costly Downtime
Ciprian Chiripuci

As businesses rely heavily on various equipment to operate smoothly, the last thing they want is unexpected equipment failure leading to costly downtime. Equipment failure not only disrupts daily operations but also results in financial losses and a negative impact on productivity. We will explore the top 10 reasons for equipment failure and provide valuable insights on how to prevent them. By understanding these factors, you can take proactive measures to ensure your equipment operates efficiently and avoid potential setbacks. So let's dive in and discover how to keep your operations running smoothly!
Lack of Proper Maintenance
One of the most common causes of equipment failure is a lack of proper maintenance. Neglecting regular maintenance tasks such as cleaning, lubrication, calibration and inspection can significantly reduce lifespan of equipment. By implementing a comprehensive maintenance schedule and adhering to it diligently, you can prevent potential failures and extend life of your equipment.
Overloading or Misuse
Overloading equipment beyond its recommended capacity or using it in unintended ways can quickly lead to failure. Each piece of equipment has its limitations and pushing them beyond those limits can cause excessive wear and tear, leading to breakdowns. Ensure that your staff is well-trained on the proper use of equipment and that they understand its limitations to avoid unnecessary failures.
Poor Quality or Incompatible Parts
Using low-quality or incompatible parts during equipment repairs or replacements can have disastrous consequences. Substandard parts may not withstand the normal wear and tear of the equipment, resulting in premature failure. Always source parts from reputable suppliers and ensure they meet required specifications to maintain the reliability and longevity of your equipment.
Environmental Factors
Environmental conditions play a significant role in equipment performance and longevity. Extreme temperatures, humidity, dust and corrosive substances can all contribute to equipment failure. Taking necessary precautions such as providing proper ventilation, using protective covers and installing equipment in suitable environments can help mitigate these risks.
Improper Installation
Improper installation can introduce various issues that may lead to equipment failure. Poor alignment, incorrect electrical connections or inadequate anchoring can put unnecessary stress on the equipment and compromise its functionality. Make sure that equipment is installed by trained professionals following manufacturer's guidelines to prevent installation-related failures.
Age and Wear
As equipment ages, it becomes more susceptible to wear and tear, making failures more likely. Components may degrade over time, leading to reduced performance and eventual failure. Keep track of the age of your equipment and consider implementing a replacement plan for aging assets to minimize risk of unexpected breakdowns.
Lack of Operator Training
Inadequate training of equipment operators can lead to errors and improper use, increasing chances of equipment failure. It is essential to provide comprehensive training programs that cover equipment operation, safety protocols and maintenance procedures. Well-trained operators are more likely to identify potential issues and take preventive measures to avoid failures.
Electrical Problems
Electrical issues such as power surges, voltage fluctuations and inadequate grounding can wreak havoc on your equipment. These problems can damage sensitive components, leading to malfunctions and failures. Investing in surge protectors, voltage stabilizers and regular electrical inspections can safeguard your equipment against electrical failures.
Lack of Documentation and Record-Keeping
Maintaining accurate documentation and records is crucial for equipment management. It allows you to track maintenance schedules, repair history and replacement parts, enabling you to identify patterns and take proactive measures to prevent failures. Implementing a robust asset management system and encouraging proper documentation practices will help you stay organized and avoid equipment-related surprises.
Lack of Emergency Preparedness
No matter how well you maintain your equipment, failures can still occur. Being prepared for such incidents can minimize downtime and mitigate impact on your operations. Develop contingency plans, create a spare parts inventory and establish relationships with reliable repair and maintenance service providers. By having a solid emergency preparedness strategy, you can quickly address failures and get back to normal operations swiftly.
Equipment failure can be a significant challenge for businesses, but it is not an insurmountable one. By understanding top 10 reasons for equipment failure and implementing preventive measures, you can minimize risks and keep your operations running smoothly. Remember to prioritize regular maintenance, train your staff, use high-quality parts and create a culture of awareness and preparedness. By doing so, you'll not only reduce downtime and save on repair costs but also enhance productivity and maintain a competitive edge in your industry. So, take the necessary steps today and safeguard your equipment for a brighter and more efficient future!
Remember, prevention is always better than cure!
Related posts
Here are some resources to help you get more out of your assets

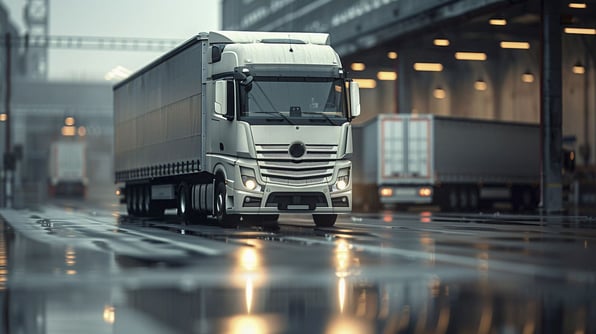
Ciprian Chiripuci
Truck Sealing in Delivery Logistics: Definition, Benefits and Best Practices
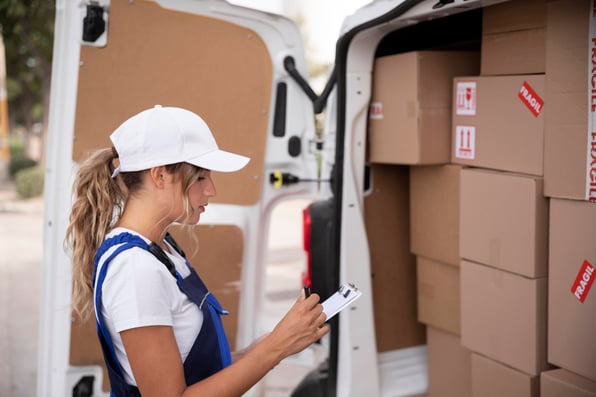
Ciprian Chiripuci
Mastering that Last Mile
READY TO TALK?