
SOP and CMMS: The Perfect Pair for Maintenance Efficiency
Ciprian Chiripuci

In the world of maintenance management, efficiency, consistency and reliability are the keys to keeping operations running smoothly. That’s where Standard Operating Procedures (SOPs) and Computerized Maintenance Management Systems (CMMS) come in. When used together, these tools help businesses standardize processes, reduce downtime, improve asset management and ensure regulatory compliance.
But how do they work together? And how can businesses implement them effectively?
In this article, we’ll break down:
✅ What SOPs and CMMS are
✅ How they complement each other
✅ Real-world examples of businesses using them successfully
✅ The key benefits of integrating SOPs into a CMMS
✅ Best practices for creating and managing SOPs with CMMS
What is a Standard Operating Procedure (SOP)?
A Standard Operating Procedure (SOP) is a detailed, written guide that outlines the step-by-step instructions for performing a specific task or process within an organization.
For maintenance teams, SOPs serve as a blueprint to ensure tasks are completed correctly, efficiently and safely. They help eliminate guesswork, reduce human error and provide consistency—whether you're training new employees or handling complex maintenance procedures.
Example of a Maintenance SOP: Air Filter Replacement for HVAC Systems
- Purpose: Ensure proper air circulation and equipment efficiency
- Frequency: Every 3 months
- Required Tools: Screwdriver, new air filter, gloves
- Steps:
- Turn off HVAC system.
- Locate and remove the old air filter.
- Insert a new filter, ensuring proper alignment.
- Secure all panels and restart the system.
- Log completion in the CMMS.
This SOP ensures that technicians follow the same process every time, preventing costly mistakes and maintaining air quality.
What is a CMMS (Computerized Maintenance Management System)?
A CMMS (Computerized Maintenance Management System) is software that helps organizations track, schedule and manage maintenance tasks for equipment and assets.
Think of CMMS as a central hub for maintenance operations, offering features like:
✅ Work order management
✅ Asset tracking
✅ Preventive maintenance scheduling
✅ Inventory and spare parts management
✅ Compliance and reporting
With a CMMS, businesses digitize and automate maintenance processes, ensuring that tasks are assigned, tracked and completed efficiently.
Example of CMMS in Action: A manufacturing plant uses a CMMS to:
- Automatically schedule preventive maintenance for machinery
- Generate work orders for technicians
- Track spare parts inventory
- Store SOPs for quick reference
- Monitor equipment performance to predict failures
By using a CMMS, maintenance teams stay organized, proactive and data-driven, reducing downtime and improving efficiency.
How SOPs and CMMS Work Together
SOPs and CMMS complement each other perfectly by combining structured procedures with digital automation.
Here’s how they work hand-in-hand:
-
SOPs Standardize Maintenance Tasks
A CMMS stores and organizes SOPs, ensuring that every technician follows the correct procedure when completing a task. Instead of relying on memory or outdated paper manuals, teams access step-by-step instructions directly from the CMMS.
👉 Example: A technician receives a work order in the CMMS to inspect a pump. The work order includes the SOP for pump inspection, ensuring that the technician follows the right steps and records the results accurately.
-
CMMS Automates SOP Execution
CMMS software automatically assigns SOPs to relevant maintenance tasks. Instead of manually distributing SOPs, managers can link them to specific work orders, preventive maintenance schedules or assets.
👉 Example: When a machine reaches 500 hours of runtime, the CMMS automatically triggers a preventive maintenance task and attaches the SOP for proper servicing.
-
Improved Compliance and Safety
SOPs help businesses meet industry regulations and CMMS makes compliance tracking effortless. Technicians can log their maintenance activities in real-time, ensuring proper documentation.
👉 Example: A hospital’s CMMS ensures that medical equipment maintenance follows strict SOPs to meet health and safety standards. Auditors can review digital logs to verify compliance.
-
Faster Training and Onboarding
New technicians learn faster when they have structured SOPs integrated into the CMMS. They can quickly access instructions, checklists and diagrams, reducing training time and increasing efficiency.
👉 Example: A new technician at a hotel facility uses the CMMS to access SOPs for elevator maintenance, ensuring proper servicing from day one.
-
Data-Driven Decision Making
By tracking SOP execution in the CMMS, managers analyze performance metrics, identify process improvements and optimize maintenance schedules.
👉 Example: A CMMS report shows that equipment failures occur frequently despite regular maintenance. Managers review SOPs and adjust procedures for better results.
Benefits of Integrating SOPs into a CMMS
1️⃣ Consistency & Quality Control – Every technician follows the same procedure, reducing errors and improving maintenance quality.
2️⃣ Increased Efficiency – SOPs speed up maintenance tasks, while CMMS automates scheduling and tracking.
3️⃣ Reduced Downtime & Costs – Preventive maintenance, guided by SOPs, prevents unexpected breakdowns and expensive repairs.
4️⃣ Better Compliance & Safety – CMMS ensures proper documentation, helping businesses meet industry regulations and safety standards.
5️⃣ Faster Training & Knowledge Retention – SOPs stored in a CMMS make it easier to train new employees and retain institutional knowledge.
Best Practices for Using SOPs with CMMS
✅ 1. Keep SOPs Clear and Concise
Write simple, step-by-step instructions that technicians can follow easily. Use bullet points, checklists and images for clarity.
✅ 2. Link SOPs to Work Orders and Assets
Ensure SOPs are easily accessible by attaching them to relevant work orders, preventive maintenance schedules and equipment records.
✅ 3. Regularly Update SOPs
Maintenance procedures evolve over time. Review and update SOPs annually or after major equipment upgrades to keep them relevant.
✅ 4. Train Employees on SOP Usage
Ensure that technicians know how to access and follow SOPs in the CMMS. Conduct training sessions and refreshers.
✅ 5. Monitor SOP Compliance with CMMS Reports
Use the CMMS to track how often SOPs are followed and identify areas for improvement.
The Power of SOPs and CMMS Together
Standard Operating Procedures (SOPs) and Computerized Maintenance Management Systems (CMMS) are a powerful combination that brings structure, efficiency and automation to maintenance management.
By integrating SOPs into a CMMS, businesses ensure consistent workflows, reduce downtime, improve compliance and streamline training.
The result? A more organized, proactive and efficient maintenance operation.
So, if your business isn’t leveraging SOPs with CMMS yet, now’s the time to start!
Image by rawpixel.com on Freepik.
Related posts
Here are some resources to help you get more out of your assets

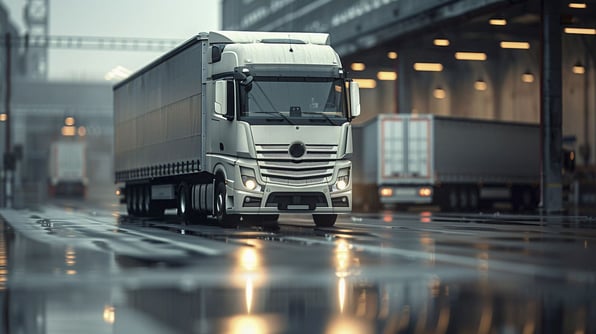
Ciprian Chiripuci
Truck Sealing in Delivery Logistics: Definition, Benefits and Best Practices
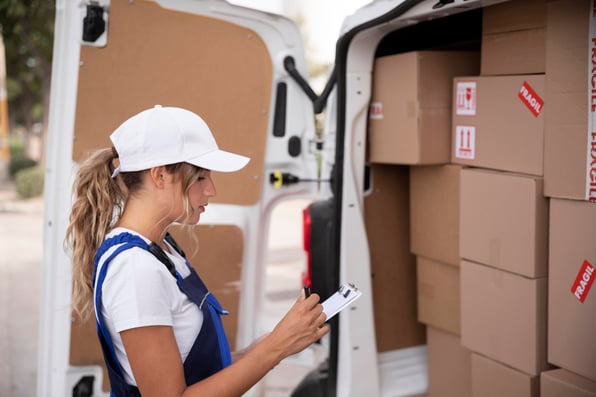
Ciprian Chiripuci
Mastering that Last Mile
READY TO TALK?