
Process Failure Mode Effect Analysis (PFMEA) and CMMS
Ciprian Chiripuci
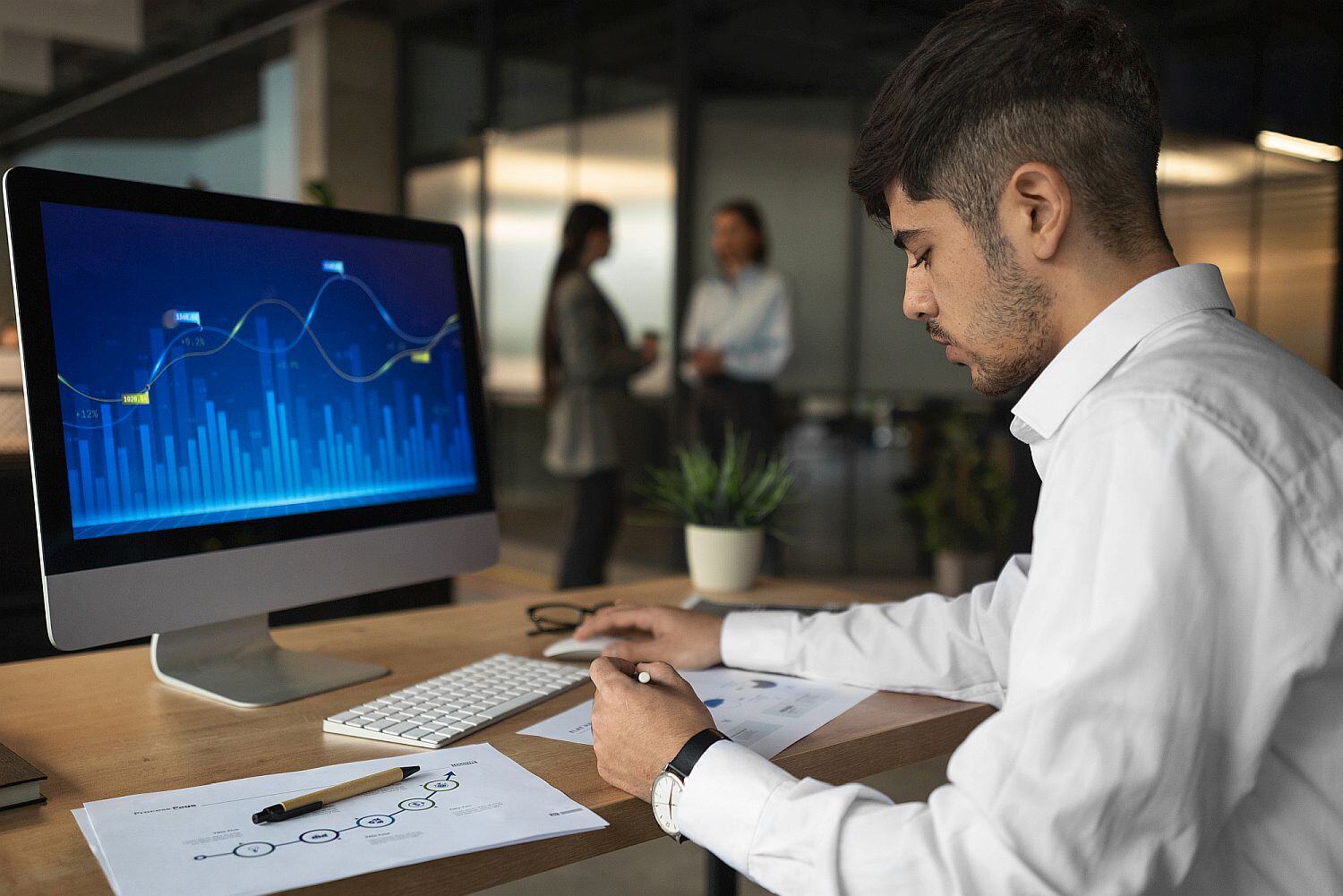
A Powerful Duo for Reliable Maintenance
If you could predict failures before they happen, wouldn’t you?
That’s exactly what Process Failure Mode Effect Analysis (PFMEA) helps businesses do. It’s a proactive risk assessment method that identifies potential failure points in a process, evaluates their impact and helps businesses prioritize preventive actions.
But PFMEA alone isn’t enough—it needs a system to track, implement and manage the corrective and preventive actions it identifies. That’s where a Computerized Maintenance Management System (CMMS) comes in. CMMS automates maintenance scheduling, tracks failure trends and ensures that maintenance teams take timely action.
When used together, PFMEA and CMMS create a powerful approach to risk reduction, equipment reliability and operational efficiency.
In this article, we’ll break down:
✅ What PFMEA is and how it works
✅ How CMMS complements PFMEA
✅ Examples of PFMEA in action
✅ Best practices for integrating PFMEA with CMMS
✅ The business benefits of using both
What is Process Failure Mode Effect Analysis (PFMEA)?
PFMEA is a structured approach used to identify and mitigate risks in a process. Originally developed in the aerospace and automotive industries, PFMEA is now widely used in manufacturing, healthcare, logistics and facility maintenance.
It focuses on answering three key questions:
1️⃣ What could go wrong? (Failure Mode)
2️⃣ What would be the consequences? (Effect)
3️⃣ How likely is it to happen and how severe would it be? (Risk Assessment)
Each failure mode is ranked using three factors:
Factor |
Description |
Scale (1-10) |
Severity (S) |
How serious the impact of failure is |
1 = Minor, 10 = Catastrophic |
Occurrence (O) |
How frequently the failure is expected to occur |
1 = Rare, 10 = Frequent |
Detection (D) |
How likely it is to detect the failure before it happens |
1 = Very likely, 10 = Impossible |
The Risk Priority Number (RPN) is calculated as:
RPN=S×O×DRPN = S \times O \times DRPN=S×O×D
Failures with high RPN scores require immediate corrective action.
How CMMS Strengthens PFMEA
A CMMS (Computerized Maintenance Management System) is software that manages maintenance schedules, tracks asset health and ensures follow-through on PFMEA findings.
While PFMEA identifies risks, CMMS ensures maintenance teams act on them effectively.
Here’s how CMMS enhances PFMEA:
✅ Automates Preventive Maintenance (PM): If PFMEA finds a high-risk failure mode (e.g., pump overheating), CMMS can schedule regular inspections, lubrication and part replacements to prevent failure.
✅ Tracks Failure Trends: CMMS logs maintenance activities, revealing patterns of failure over time. This helps businesses update PFMEA results with real-world data.
✅ Reduces Downtime: By acting on failure risks before they cause breakdowns, CMMS keeps equipment running smoothly and minimizes costly disruptions.
✅ Ensures Compliance: For industries like food processing, pharmaceuticals and aviation, CMMS helps track preventive actions, ensuring compliance with regulatory requirements.
✅ Improves Spare Parts Management: CMMS ensures that critical spare parts identified in PFMEA are available when needed, reducing repair delays.
Examples: PFMEA + CMMS in Action
Example 1: Preventing HVAC Failures in a Manufacturing Plant
Scenario:
A large manufacturing plant relies on industrial HVAC systems to maintain optimal working conditions. A breakdown in HVAC could lead to equipment overheating, product defects and lost production hours.
PFMEA Findings:
- Failure Mode: HVAC compressor failure
- Effect: Increased temperature, decreased product quality
- Severity (S): 8 (high impact on operations)
- Occurrence (O): 6 (recurring issue)
- Detection (D): 5 (some warning signs exist)
- RPN Score: 240 (requires immediate action!)
Solution Using CMMS:
- CMMS schedules routine compressor maintenance (lubrication, filter replacement).
- Sensors track temperature changes and trigger work orders before failure occurs.
- Parts inventory is optimized to keep replacement compressors in stock.
Result: HVAC failures are reduced by 80%, preventing production delays and saving thousands in repair costs.
Example 2: Reducing Downtime in a Logistics Hub
Scenario:
A logistics company relies on a fleet of conveyor belts to sort packages. Unplanned breakdowns delay shipments, affecting customer satisfaction.
PFMEA Findings:
- Failure Mode: Conveyor motor overheating
- Effect: Sorting system failure, shipment delays
- Severity (S): 9 (high impact on deliveries)
- Occurrence (O): 7 (common issue)
- Detection (D): 4 (failure is often missed until too late)
- RPN Score: 252 (requires urgent attention!)
Solution Using CMMS:
- CMMS automates lubrication and inspection schedules.
- Infrared sensors monitor motor temperature, triggering alerts before failure.
- Maintenance teams receive automatic work orders when early warning signs appear.
Result: Conveyor downtime drops by 60%, keeping shipments on track.
Best Practices for Integrating PFMEA with CMMS
🔹 1. Conduct PFMEA at Least Annually
Regularly review and update risk assessments based on new failures or operational changes.
🔹 2. Automate Preventive Maintenance with CMMS
Set up scheduled PM tasks to address high-RPN risks before failures occur.
🔹 3. Track Failures and Update PFMEA
Use CMMS reports to identify trends in failure data and refine PFMEA scoring.
🔹 4. Use IoT Sensors for Real-Time Monitoring
Pair CMMS with IoT sensors to detect early warning signs and trigger automated work orders.
🔹 5. Train Maintenance Teams on PFMEA Findings
Ensure technicians understand why certain tasks are critical and how they prevent major failures.
🔹 6. Optimize Spare Parts Inventory
Use CMMS to stock critical components identified in PFMEA, reducing downtime when repairs are needed.
The Business Benefits of PFMEA + CMMS
✅ Fewer Equipment Failures → Increased reliability and uptime
✅ Lower Maintenance Costs → Preventive maintenance is cheaper than emergency repairs
✅ Improved Safety → Identifies risks before they lead to accidents
✅ Regulatory Compliance → Ensures businesses meet industry safety standards
✅ Better Decision-Making → Data-driven insights from CMMS refine maintenance strategies
A Winning Combination for Business Success
Process Failure Mode Effect Analysis (PFMEA) and CMMS aren’t just maintenance tools—they’re strategic assets that help businesses predict failures, reduce costs and improve reliability.
By integrating PFMEA’s risk assessment approach with CMMS’s automation and tracking capabilities, businesses can achieve proactive, data-driven maintenance management.
🚀 Is your company leveraging PFMEA and CMMS effectively? If not, now is the time to start!
Image by Freepik.
Related posts
Here are some resources to help you get more out of your assets

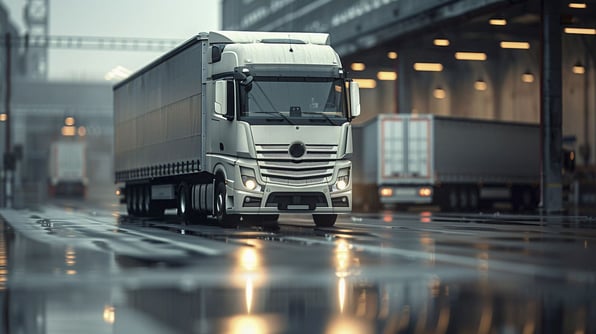
Ciprian Chiripuci
Truck Sealing in Delivery Logistics: Definition, Benefits and Best Practices
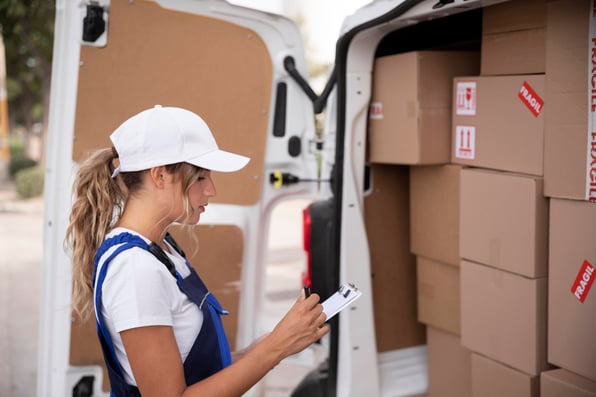
Ciprian Chiripuci
Mastering that Last Mile
READY TO TALK?