
Preventive Maintenance Checklists
Ciprian Chiripuci
.jpg)
In today's fast-paced business environment, ensuring the smooth operation of equipment and machinery is essential for maximizing productivity and minimizing downtime. Preventive maintenance is a proactive approach that helps organizations identify and address potential issues before they escalate into costly breakdowns. A critical component of preventive maintenance is the use of comprehensive checklists that guide technicians through routine inspections and maintenance tasks. In this article, we'll explore the importance of preventive maintenance checklists, their benefits, best practices and provide industry insights to help you establish a robust maintenance program that keeps your equipment running smoothly.
Understanding Preventive Maintenance Checklists
The Role of Preventive Maintenance Checklists: Preventive maintenance checklists are systematic documents that outline steps and tasks required for regular equipment inspections and maintenance activities. These checklists serve as a roadmap for technicians, ensuring that no critical components or maintenance tasks are overlooked. By following these checklists, businesses can maintain equipment reliability, extend the lifespan of assets and reduce risk of unexpected failures.
Benefits of Using Preventive Maintenance Checklists
a) Minimize Downtime: Regular inspections and maintenance tasks help identify and address issues before they cause major breakdowns, minimizing equipment downtime and production disruptions. b) Enhanced Equipment Performance: Timely maintenance keeps equipment in optimal condition, leading to improved performance, efficiency and output quality.c) Cost Savings: Preventive maintenance reduces the need for expensive emergency repairs, extends equipment lifespan and minimizes risk of costly production delays.
d) Safety and Compliance: Regular inspections ensure that equipment meets safety standards and regulatory requirements, protecting both employees and the organization from potential liabilities.
Creating Effective Preventive Maintenance Checklists
Identify Equipment and Components
Begin by identifying the equipment and its critical components that require regular inspections and maintenance. This can include mechanical, electrical and electronic systems.
Determine Inspection Intervals
Determine the appropriate inspection intervals based on equipment manufacturer recommendations, industry standards and historical data. Consider factors such as equipment usage, operating conditions and criticality.
Define Inspection Tasks
Break down the inspection process into specific tasks and activities. Include visual inspections, component checks, lubrication requirements, calibration and any other maintenance tasks relevant to the equipment.
Establish Task Frequencies
Assign appropriate frequencies to each task, whether it's daily, weekly, monthly or annually. This ensures that all maintenance activities are performed consistently and at the right intervals.
Provide Clear Instructions
Write clear and concise instructions for each task, detailing the steps to be followed, safety precautions and any necessary documentation or equipment needed.
Incorporate Documentation and Reporting
Include sections for technicians to record inspection results, findings and any corrective actions taken. This documentation provides valuable data for future analysis, trend identification and decision-making.
Best Practices for Implementing Preventive Maintenance Checklists
Training and Communication
Ensure that technicians receive thorough training on using preventive maintenance checklists effectively. Encourage open communication between maintenance teams and other stakeholders to address any concerns or suggestions for improvement.
Regular Review and Updates
Periodically review and update the preventive maintenance checklists to incorporate new equipment, changes in procedures or lessons learned from previous inspections. Regular feedback from technicians can help refine and improve the checklists over time.
Utilize Technology
Consider leveraging maintenance management software or computerized maintenance management systems (CMMS) to streamline checklist creation, scheduling and documentation. These tools can automate notifications, generate reports and provide valuable insights for maintenance planning and decision-making.
Industry Insights and Statistics
Importance of Preventive Maintenance
According to a survey conducted by Plant Engineering magazine organizations that implemented preventive maintenance programs reported a 28% reduction in maintenance costs and a 30% decrease in equipment downtime.
Impact on Energy Efficiency
Properly maintained equipment is more energy-efficient. U.S. Department of Energy estimates that well-maintained HVAC systems alone can reduce energy consumption by up to 20%.
Compliance and Regulatory Requirements
Industries such as healthcare, manufacturing and transportation have specific regulatory requirements for equipment maintenance. Non-compliance can lead to penalties, reputational damage and legal liabilities.
Preventive maintenance checklists are invaluable tools for ensuring efficient equipment management, reducing downtime and maximizing operational productivity. By implementing comprehensive checklists organizations can stay ahead of potential issues, improve equipment performance and minimize costly repairs. Remember to customize checklists to suit your specific equipment and industry requirements, regularly review and update them and leverage technology for streamlined maintenance operations. With a proactive approach to preventive maintenance, your organization can reap the benefits of enhanced equipment reliability, increased lifespan and improved operational efficiency.
Related posts
Here are some resources to help you get more out of your assets

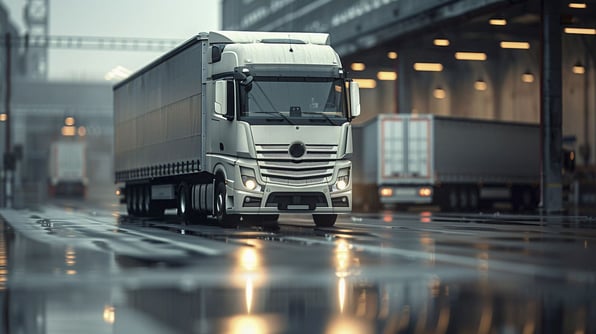
Ciprian Chiripuci
Truck Sealing in Delivery Logistics: Definition, Benefits and Best Practices
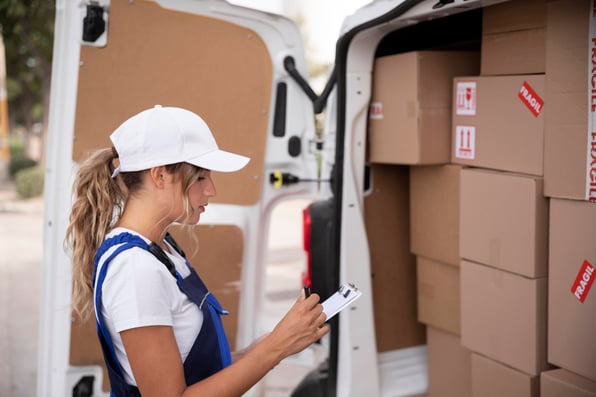
Ciprian Chiripuci
Mastering that Last Mile
READY TO TALK?