
Predictive Maintenance: Unveiling the Future of Equipment Management
Ciprian Chiripuci
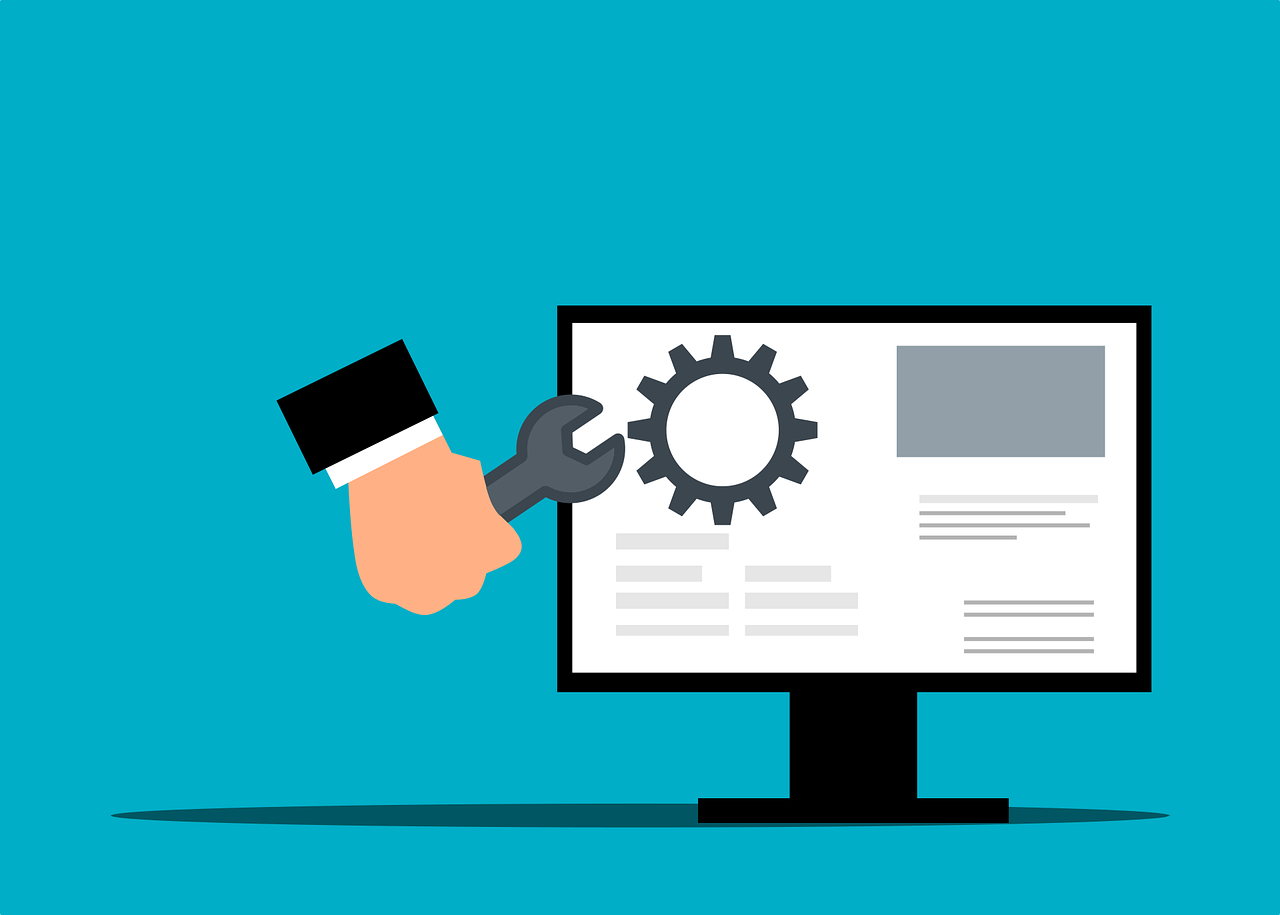
In the world of business, equipment downtime can be a major setback, leading to lost productivity, increased costs and customer dissatisfaction. This is where predictive maintenance comes into play. By harnessing the power of technology and data, predictive maintenance revolutionizes equipment management by proactively identifying potential failures and addressing them before they occur. In this article, we will delve into the concept of predictive maintenance, exploring its benefits, implementation strategies and the transformative impact it can have on businesses.
Understanding Predictive Maintenance
Predictive maintenance is a proactive approach to equipment management that utilizes advanced technologies and data analysis to predict when equipment failures are likely to occur. By monitoring the condition, performance and usage patterns of equipment, predictive maintenance leverages algorithms and machine learning to identify potential issues and schedule maintenance tasks before breakdowns happen. This shift from reactive to proactive maintenance empowers businesses to maximize equipment uptime, optimize maintenance costs and improve operational efficiency.
Benefits of Predictive Maintenance
Minimized Downtime:
By predicting failures before they happen, predictive maintenance allows businesses to schedule maintenance during planned downtime, minimizing unexpected equipment failures and reducing costly interruptions to operations.
Improved Productivity:
Predictive maintenance helps businesses maintain equipment in optimal working condition, ensuring consistent performance and minimizing disruptions. This leads to improved productivity and efficiency across the organization.
Cost Optimization:
Traditional reactive maintenance can result in unnecessary repairs and replacement costs. Predictive maintenance, on the other hand, enables businesses to plan maintenance activities in a cost-effective manner, optimizing the use of resources and reducing overall maintenance expenses.
Enhanced Equipment Lifespan:
By monitoring and addressing equipment issues in a timely manner, predictive maintenance can extend the lifespan of critical assets. This reduces need for premature replacements and capital expenditures, saving businesses significant costs in the long run.
Increased Safety:
Malfunctioning equipment poses safety risks to both employees and customers. Predictive maintenance helps identify potential safety hazards and allows businesses to proactively address them, ensuring a safe working environment.
Implementing Predictive Maintenance
Data Collection and Monitoring:
The foundation of predictive maintenance lies in the collection and analysis of relevant data. Implement sensors, IoT devices or other monitoring systems to gather real-time data on equipment performance, operating conditions and usage patterns.
Data Analysis and Modeling:
Utilize advanced analytics tools and machine learning algorithms to analyze the collected data and develop models that can identify patterns, anomalies and potential failure indicators.
Establish Baselines and Thresholds:
Determine the baseline performance metrics for your equipment and set thresholds that trigger maintenance actions when deviations are detected. These thresholds can be based on factors such as vibration levels, temperature variations or other specific performance indicators.
Integration with Maintenance Management Systems:
Integrate your predictive maintenance system with your existing maintenance management software to streamline workflows and ensure seamless communication between predictive alerts and maintenance tasks.
Continuous Improvement:
Predictive maintenance is an iterative process. Regularly assess performance of your predictive models, fine-tune algorithms and incorporate new data sources to improve accuracy and reliability.
The Future of Predictive Maintenance
As technology advances and data-driven insights become more refined, the future of predictive maintenance holds even greater promise. Here are a few trends shaping the future of this transformative practice:
Artificial Intelligence and Machine Learning:
AI and machine learning algorithms will continue to evolve, enabling more accurate predictions and deeper insights into equipment performance.
Integration of IoT and Edge Computing:
Integration of IoT devices and edge computing will allow real-time data processing and analysis, reducing latency and enabling faster decision-making for maintenance actions.
Predictive Analytics for Proactive Decision-Making:
Predictive analytics will extend beyond maintenance tasks, enabling businesses to make proactive decisions related to equipment replacement, process optimization and resource allocation.
Digital Twins:
Digital twin technology, creating virtual replicas of physical assets, will play a crucial role in predictive maintenance. Digital twins can simulate equipment behavior, predict failures and optimize maintenance strategies.
Predictive maintenance is a game-changer for businesses, transforming equipment management from a reactive and costly approach to a proactive and efficient one. By harnessing the power of technology, data analysis and predictive algorithms, businesses can minimize downtime, optimize costs, enhance safety and extend the lifespan of their critical assets. Embrace the future of equipment management by implementing predictive maintenance and unlock the full potential of your business.
Related posts
Here are some resources to help you get more out of your assets

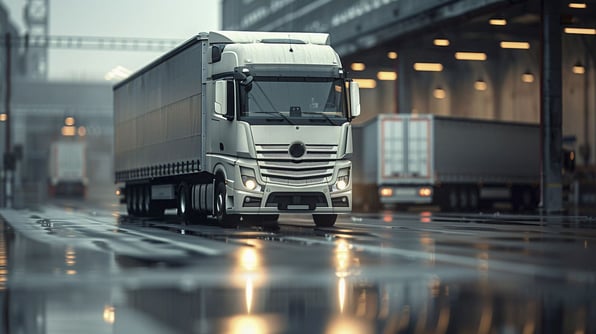
Ciprian Chiripuci
Truck Sealing in Delivery Logistics: Definition, Benefits and Best Practices
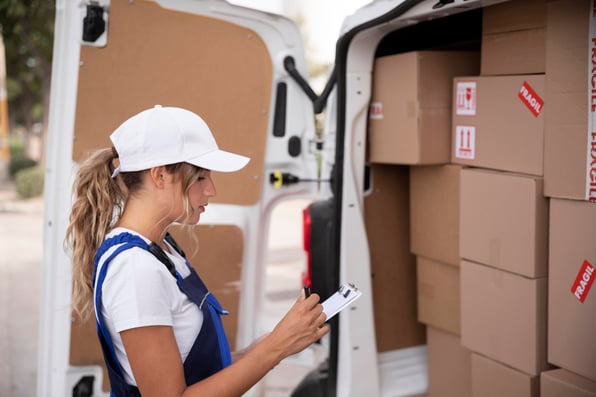
Ciprian Chiripuci
Mastering that Last Mile
READY TO TALK?