
Navigating Reliability with the P-F Curve
Ciprian Chiripuci
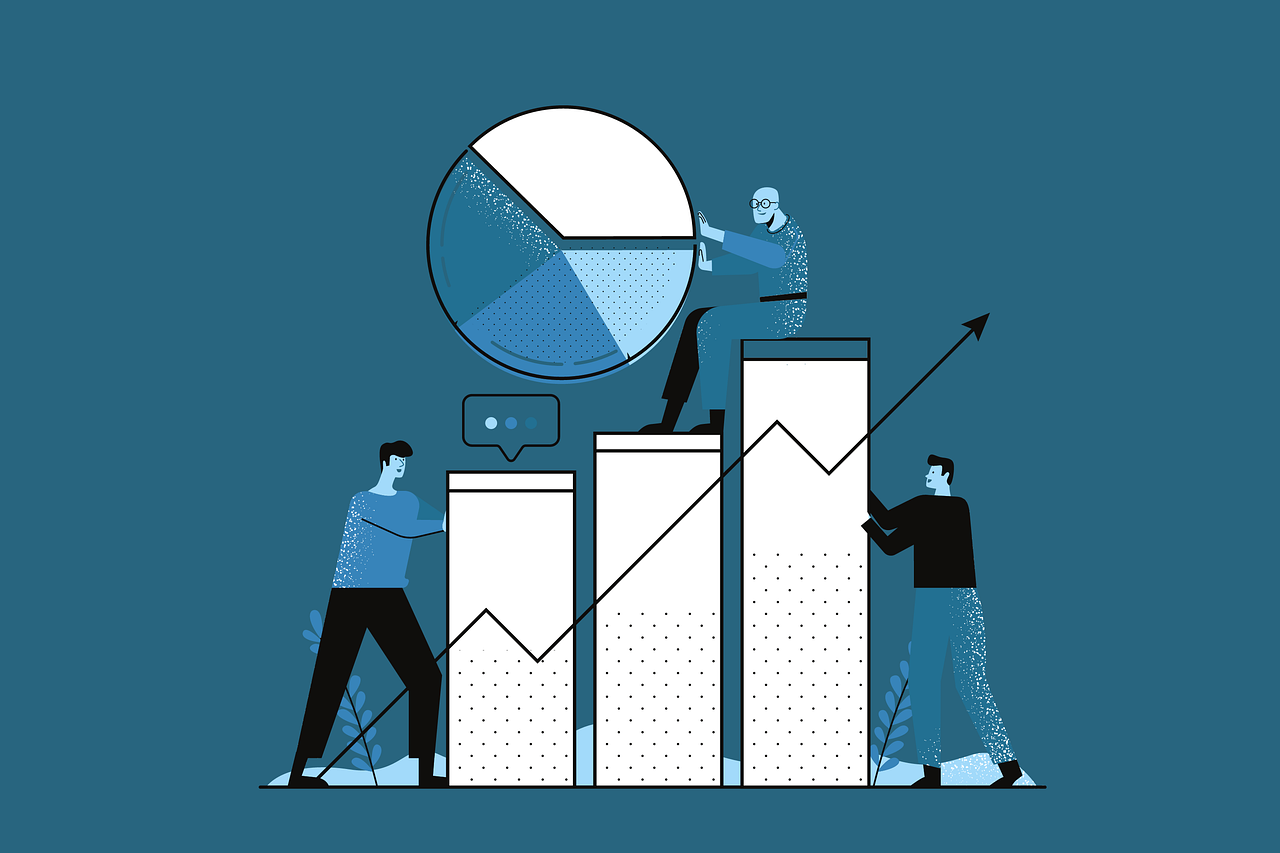
Downtime and unexpected breakdowns can lead to severe financial and operational setbacks for any business. This is where the P-F Curve, a powerful predictive maintenance tool, comes into play. Let’s explore its benefits and best practices.
Understanding the P-F Curve
The P-F Curve, short for Potential Failure - Functional Failure Curve, is a concept used in predictive maintenance to predict when equipment will fail and to schedule maintenance activities proactively. It's a vital tool that helps organizations save time, money and resources by addressing issues before they result in costly breakdowns.
Situational Example: Imagine you run a manufacturing facility. One of your key production machines has been showing signs of wear and tear, but you're unsure when it will fail. The P-F Curve can help you pinpoint the potential failure (P) and schedule maintenance before a catastrophic breakdown occurs.
The Structure of the P-F Curve
The P-F Curve consists of two critical points:
- P - Potential Failure Point: This is the moment when an issue or deterioration becomes noticeable, even if the equipment is still functioning adequately. Detecting potential failures is essential for predictive maintenance.
- F - Functional Failure Point: This is when the equipment reaches a state of complete failure. At this stage, production is disrupted and expensive emergency repairs are often required.
Benefits of the P-F Curve:
Now, let's delve into the numerous advantages the P-F Curve offers to businesses.
-
Cost Savings
By identifying potential failures before they lead to functional failures, you can avoid costly emergency repairs, downtime and production losses.
-
Increased Equipment Lifespan
Timely maintenance can extend life of your equipment, reducing need for frequent replacements.
-
Enhanced Safety
Proactive maintenance reduces the risk of accidents and injuries associated with malfunctioning equipment.
-
Improved Asset Management
The P-F Curve aids in optimizing resource allocation by scheduling maintenance activities precisely when needed.
Best Practices for Implementing the P-F Curve
To harness the full potential of the P-F Curve, here are some best practices to keep in mind:
-
Data Collection and Analysis
Start by gathering data on equipment performance, failure history and relevant sensor data. This data is crucial for establishing accurate P-F Curves.
-
Define P-F Thresholds
Clearly define your Potential Failure and Functional Failure thresholds for each piece of equipment. This ensures consistency in your maintenance approach.
-
Condition Monitoring
Invest in advanced condition monitoring technologies such as vibration analysis, thermal imaging or oil analysis. These tools provide real-time insights into your equipment's health.
-
Regular Inspections
Regularly inspect equipment to detect any early warning signs. Train your maintenance team to recognize these signals.
-
Proactive Scheduling
Use predictive maintenance software to schedule maintenance activities based on the P-F Curves. This software can optimize maintenance intervals and help with resource planning.
-
Documentation
Keep detailed records of maintenance activities, including P-F Curve data, to refine your maintenance strategy continually.
-
Continuous Improvement
Periodically review and update P-F Curves based on changing equipment conditions, performance and the evolving needs of your organization.
Real-Life Applications of the P-F Curve
The P-F Curve can be applied to various industries. Here are some industry-specific examples:
Manufacturing
Predict when a machine's bearings might fail and replace them proactively, preventing costly downtime.
Oil and Gas
Monitor corrosion rate of pipelines and schedule maintenance before it becomes critical, ensuring safe operations.
Aviation
Use the P-F Curve to anticipate engine component failures and prevent in-flight emergencies.
Healthcare
Predict when a critical medical device, like an MRI machine, may fail to avoid delays in patient care.
The P-F Curve is an indispensable tool for ensuring the reliability and longevity of equipment across various industries. By understanding its principles, implementing best practices and embracing its benefits, businesses can significantly reduce downtime, save on maintenance costs and enhance overall operational efficiency.
Embrace the P-F Curve and embark on a journey towards equipment health and business prosperity. Remember, the key to success is knowing when to act before it's too late.
Related posts
Here are some resources to help you get more out of your assets

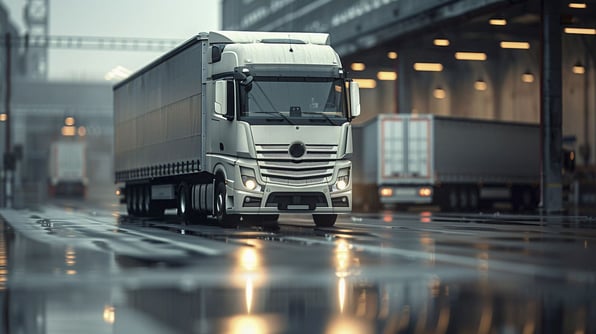
Ciprian Chiripuci
Truck Sealing in Delivery Logistics: Definition, Benefits and Best Practices
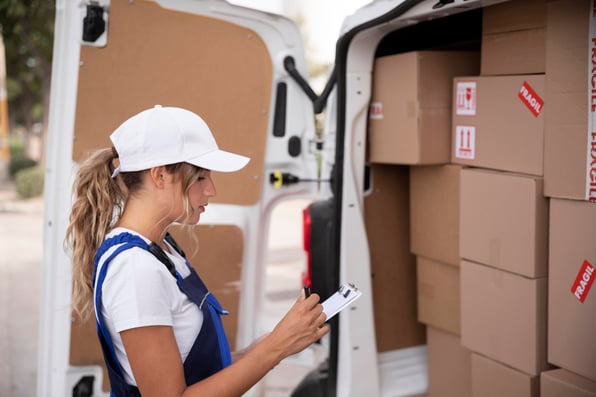
Ciprian Chiripuci
Mastering that Last Mile
READY TO TALK?