
Maximizing Efficiency and Uptime: The Power of Reliability-Centered Maintenance (RCM)
Ciprian Chiripuci
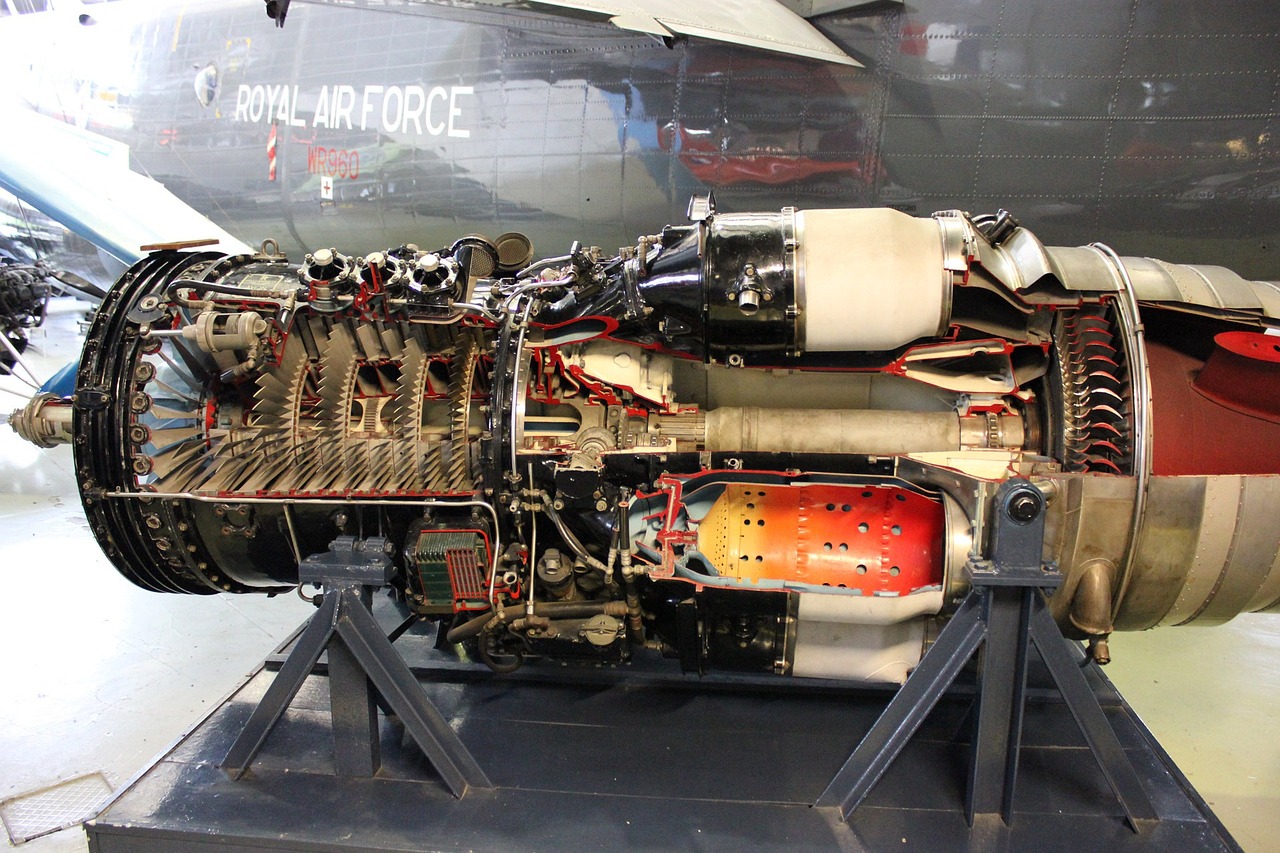
In the fast-paced world of business, every minute of downtime can result in lost profits, eroding customer trust and jeopardizing long-term success. The need for effective maintenance strategies is evident and one approach that has gained prominence is Reliability-Centered Maintenance (RCM).
Understanding Reliability-Centered Maintenance (RCM)
Reliability-Centered Maintenance, often abbreviated as RCM, is a systematic approach to managing maintenance in a way that ensures assets’ reliability and performance, while simultaneously optimizing maintenance costs. RCM originated in the aerospace industry and has since been adapted across various sectors, including manufacturing, energy and transportation.
At its core, RCM is a proactive strategy that aims to identify the most appropriate maintenance tasks for each piece of equipment, based on a thorough understanding of its function and performance requirements. It recognizes that not all assets require the same level of attention and that over-maintaining can be as detrimental as under-maintaining.
Possible Situations Where RCM Excels
-
Aircraft Maintenance in the Aviation Industry
Imagine you are the manager of an airline maintenance department. Your primary concern is ensuring the safety and reliability of your aircraft while managing the immense cost associated with regular maintenance checks. RCM can be your guiding star. By analyzing the critical components of the aircraft and tailoring maintenance tasks based on their usage and wear patterns, RCM helps you reduce downtime and save on maintenance costs without compromising safety.
-
Manufacturing Equipment Maintenance
In a bustling manufacturing facility, your production lines are the lifeblood of your business. Any unexpected downtime can translate to huge losses. RCM allows you to create a well-structured maintenance plan, addressing specific needs of each machine. By monitoring equipment health and predicting failures, you can schedule maintenance during planned shutdowns, avoiding costly unplanned stops.
-
Power Plant Operation
Operating a power plant is a massive undertaking and power generation equipment must run efficiently 24/7. RCM can be instrumental in prioritizing maintenance tasks for critical components like turbines, generators and transformers. It ensures these components receive the right attention at the right time, maximizing uptime and preventing costly failures.
Benefits of RCM
-
Improved Equipment Reliability
RCM's focus on identifying and addressing the most critical maintenance needs leads to increased equipment reliability. This means fewer breakdowns, reduced downtime and more consistent performance.
-
Cost Reduction
By eliminating unnecessary maintenance and targeting the most critical areas, RCM reduces operational costs, including labor, spare parts and downtime-related losses.
-
Safety Enhancement
RCM emphasizes the safety of operations by ensuring that maintenance tasks are designed to mitigate risks and comply with safety standards.
-
Extended Equipment Life
Properly maintained equipment lasts longer. RCM helps extend the life of your assets, reducing the need for costly replacements.
-
Regulatory Compliance
In highly regulated industries, like healthcare or aviation, adhering to maintenance standards is critical. RCM helps organizations meet regulatory requirements efficiently.
Best Practices for Implementing RCM
-
Asset Prioritization
Identify critical assets that have the most significant impact on your operations and focus your RCM efforts on them.
-
Cross-Functional Teams
Engage experts from different departments in the RCM process to gain a comprehensive understanding of asset requirements and performance expectations.
-
Data-Driven Decision Making
Use data and predictive maintenance tools to inform your decisions. Collect and analyze equipment performance data to predict failures and take preventive action.
-
Continuous Improvement
RCM is an evolving process. Regularly review and update your maintenance strategies based on changing equipment conditions and industry developments.
-
Training and Knowledge Sharing
Invest in training and knowledge sharing to ensure that your teams understand and can implement RCM effectively.
-
Use of Technology
Leverage cutting-edge maintenance management software and technologies, such as Internet of Things (IoT) sensors and predictive analytics, to streamline RCM processes and enhance data-driven decision-making.
Reliability-Centered Maintenance is not just a buzzword; it's a game-changer in the world of maintenance and asset management. By tailoring maintenance practices to the specific needs of critical assets, it maximizes reliability, minimizes costs and enhances safety. To harness the full potential of RCM organizations should adopt best practices, engage cross-functional teams and embrace data-driven decision-making. With RCM as your guiding principle, you can keep your operations running smoothly and achieve new heights of efficiency and profitability. Embrace the power of RCM and you'll be on the path to lasting success in today's competitive business landscape.
Related posts
Here are some resources to help you get more out of your assets

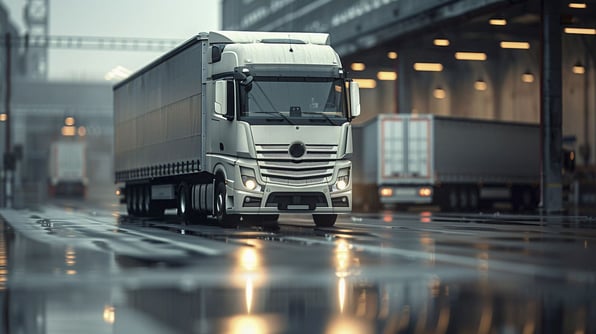
Ciprian Chiripuci
Truck Sealing in Delivery Logistics: Definition, Benefits and Best Practices
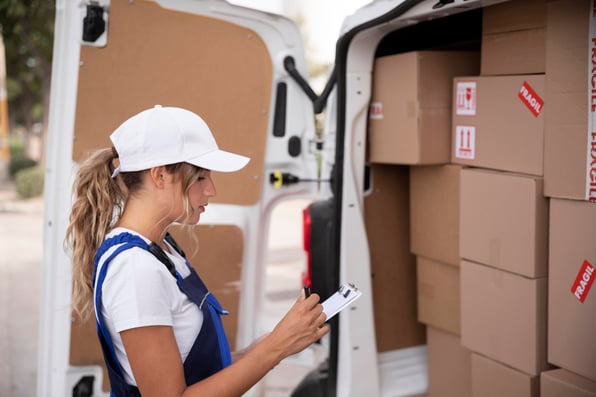
Ciprian Chiripuci
Mastering that Last Mile
READY TO TALK?