
Maintenance Checklists: Ensuring Smooth Operations and Preventing Costly Downtime
Ciprian Chiripuci
.jpg)
One effective tool to keep operations running smoothly to maintain productivity and minimize costly downtime is a comprehensive maintenance checklist. By implementing regular maintenance checklists, businesses can proactively address potential issues, ensure equipment longevity and optimize performance. In this article, we will delve into the importance of maintenance checklists.
Understanding Maintenance Checklists
1.1 What is a Maintenance Checklist?
A maintenance checklist is a systematic guide that outlines a series of tasks and inspections required to keep equipment, machinery or facilities in optimal condition. It serves as a reminder for maintenance teams to perform routine checks, identify potential problems and take appropriate actions.
1.2 Importance of Maintenance Checklists
By implementing maintenance checklists, businesses can benefit in the following ways:
Preventing Costly Downtime
Regular maintenance helps identify and address potential issues before they escalate into significant problems that could halt operations. By minimizing unplanned downtime, businesses can avoid costly disruptions and loss of revenue.
Extending Equipment Lifespan
Routine maintenance, guided by checklists, ensures that equipment is serviced and repaired as needed. This proactive approach maximizes the longevity of assets, reducing the need for frequent replacements.
Enhancing Operational Efficiency
Maintenance checklists help optimize equipment performance by ensuring all components are operating at peak levels. This leads to improved efficiency, reduced energy consumption and higher overall productivity.
Ensuring Safety and Compliance
Maintenance checklists incorporate safety inspections, ensuring that equipment adheres to industry regulations and standards. This reduces risk of accidents or injuries, protecting both employees and organization.
Practical Examples of Maintenance Checklists
Facility Maintenance Checklist Example tasks for a facility maintenance checklist could include:
- Inspecting electrical systems, ensuring proper grounding and functioning of switches and outlets.
- Checking HVAC systems for proper airflow, temperature control and filter replacement.
- Examining plumbing systems for leaks, blockages and water pressure issues.
- Assessing the condition of flooring, walls and ceilings, addressing any repairs or maintenance needs.
- Verifying functionality of fire safety equipment, such as alarms and extinguishers.
Equipment Maintenance Checklist For equipment maintenance, checklist could include:
- Lubricating moving parts and ensuring proper alignment.
- Cleaning filters, vents and cooling systems to prevent overheating.
- Checking for signs of wear and tear, such as frayed cables or damaged belts.
- Verifying accuracy of the sensors, gauges and control panels.
- Calibrating equipment to maintain accuracy and precision.
Best Practices for Implementing Maintenance Checklists
Create Detailed Checklists
Develop comprehensive checklists that cover all necessary tasks, inspections and safety measures specific to each equipment type or facility. Include step-by-step instructions to ensure consistency in execution.
Set Appropriate Frequencies
Determine optimal maintenance intervals for each item on the checklist, considering factors such as manufacturer recommendations, equipment usage patterns and environmental conditions.
Assign Responsibility
Clearly define roles and responsibilities for executing maintenance tasks. Assign dedicated team members or technicians who are accountable for completing specific checklists.
Utilize Technology
Leverage digital tools and maintenance management software to streamline the checklist creation, tracking and reporting processes. This enables real-time data capture, task assignment and analytics for more efficient maintenance operations.
Document and Track
Maintain a record of all completed checklists, including dates, findings and actions taken. This documentation provides a historical reference for analysis, compliance audits and identifying recurring issues.
Regular Review and Improvement
Continuously evaluate effectiveness of maintenance checklists and incorporate feedback from maintenance teams. Update checklists periodically to reflect evolving maintenance requirements and lessons learned.
Maintenance checklists are indispensable tools for businesses to proactively manage their equipment, facilities and operations. By implementing regular maintenance routines and following best practices organizations can prevent costly downtime, extend equipment lifespans, enhance operational efficiency and ensure safety and compliance. Whether it's a facility or equipment maintenance checklist, the key lies in creating comprehensive, detailed checklists and leveraging technology to streamline processes. By prioritizing proactive maintenance, businesses can minimize disruptions, optimize productivity and stay ahead in today's competitive landscape.
Related posts
Here are some resources to help you get more out of your assets

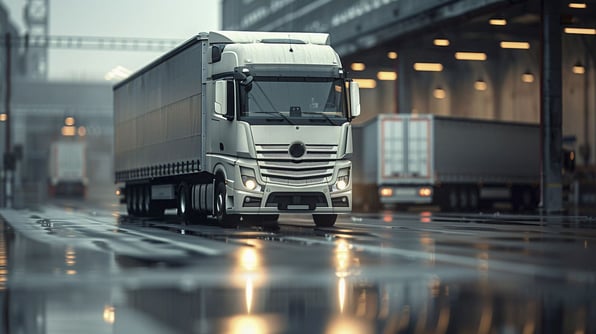
Ciprian Chiripuci
Truck Sealing in Delivery Logistics: Definition, Benefits and Best Practices
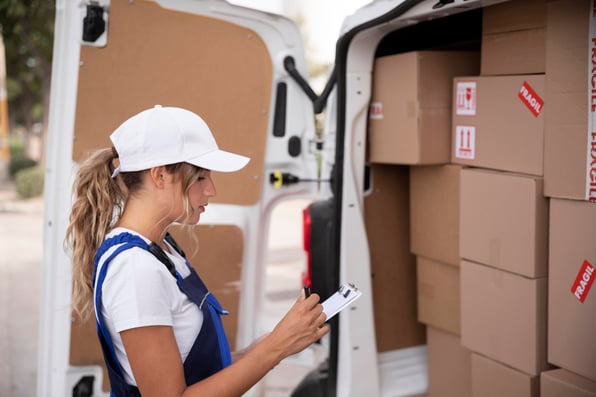
Ciprian Chiripuci
Mastering that Last Mile
READY TO TALK?