
CMMS for building maintenance
Ciprian Chiripuci
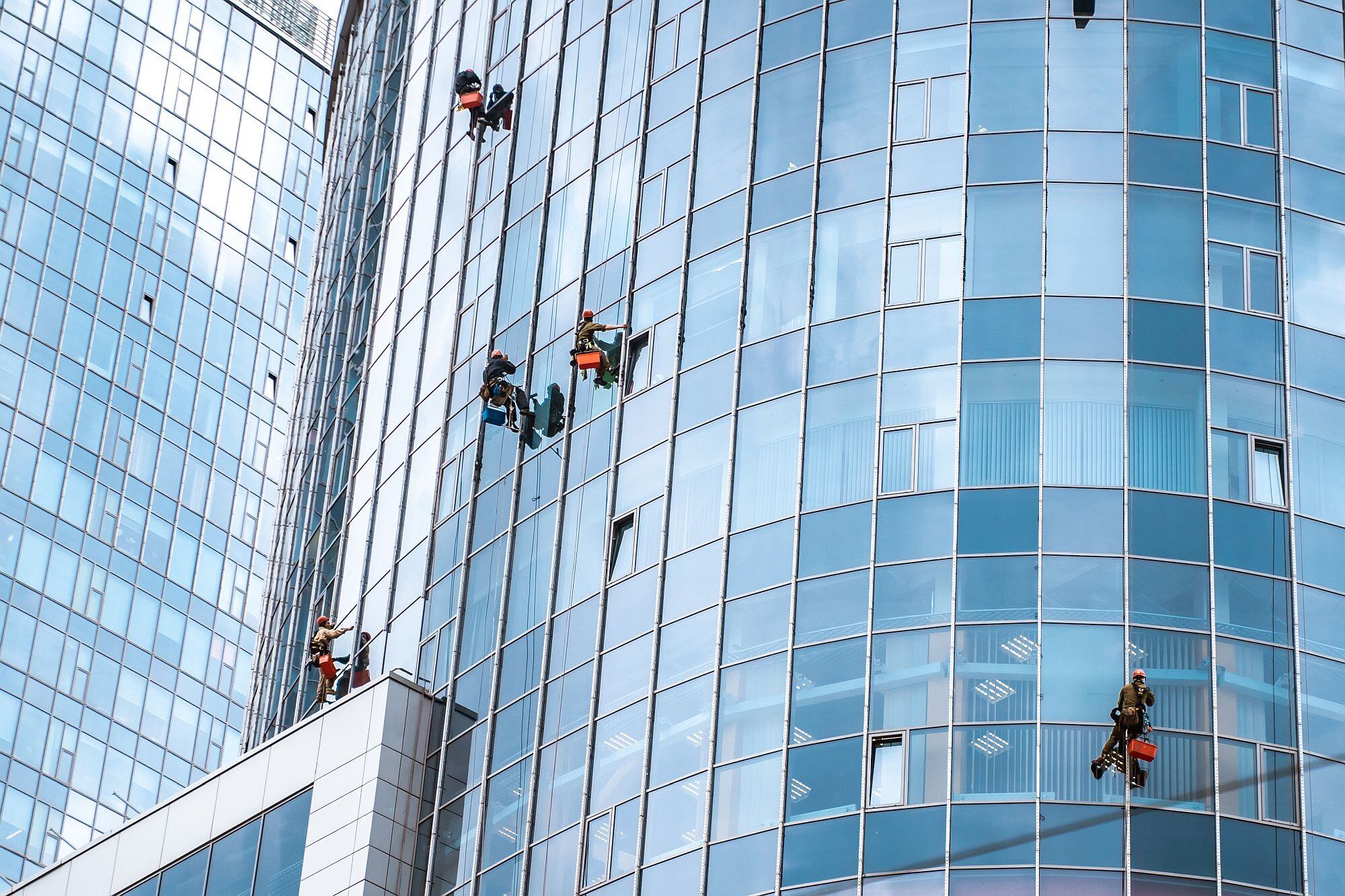
Keeping a building in top shape isn’t just about fixing things when they break. It’s about preventative care, cost efficiency and keeping everything running smoothly—from HVAC systems to elevators, lighting, plumbing and even landscaping.
If you manage a commercial building, office space, manufacturing facility, hotel or residential complex, you know that maintenance can quickly become overwhelming. That’s where a CMMS (Computerized Maintenance Management System) comes in.
A CMMS helps streamline maintenance tasks, automate work orders, track assets and improve overall efficiency—making life easier for maintenance teams and facility managers alike. But how exactly does it work and why is it crucial for building maintenance?
What is CMMS and How Does It Work?
A CMMS (Computerized Maintenance Management System) is software that helps organizations manage maintenance operations efficiently. It keeps track of:
- Work orders (scheduled and reactive maintenance)
- Equipment and asset history
- Inventory and spare parts management
- Preventative maintenance schedules
- Compliance with safety regulations
A CMMS allows maintenance teams to:
✅ Log and track work orders digitally instead of using paper or spreadsheets
✅ Schedule preventative maintenance to reduce unexpected failures
✅ Monitor asset conditions to extend their lifespan
✅ Automate maintenance requests, ensuring quick response times
In short, CMMS takes the chaos out of maintenance and helps facility managers stay ahead of problems instead of reacting to emergencies.
Why is CMMS Important for Building Maintenance?
If you manage a large facility or multiple buildings, maintenance tasks can pile up fast. Without an organized system, maintenance can become:
🔴 Reactive rather than proactive (leading to costly breakdowns)
🔴 Time-consuming (because work orders get lost or forgotten)
🔴 Expensive (due to emergency repairs and inefficient processes)
🔴 Compliance risk (failing to meet safety and building regulations)
A CMMS solves these challenges by keeping everything organized in one system. Here’s why it’s a must-have for building maintenance:
-
Reduces Equipment Downtime
Regular maintenance prevents major breakdowns. CMMS schedules preventative maintenance, reducing the risk of failures in crucial systems like HVAC, plumbing and electrical.
👉 Example: A shopping mall uses CMMS to schedule HVAC maintenance every three months. Because the system automatically alerts the team, they prevent costly failures that could disrupt business.
-
Improves Work Order Management
A CMMS automates and tracks work orders, ensuring maintenance tasks are assigned, completed and documented efficiently.
👉 Example: A hotel receives 20+ maintenance requests daily (e.g., a leaky faucet, broken elevator or air conditioning issue). A CMMS automatically routes the request to the right technician and logs the completion, eliminating paperwork and delays.
-
Saves Money on Repairs
Planned maintenance is always cheaper than emergency repairs. CMMS helps avoid costly downtime and unexpected expenses.
👉 Example: A manufacturing plant uses CMMS to track machine maintenance. Instead of waiting for a motor to fail (costing thousands in repairs and downtime), they schedule proactive servicing, saving money in the long run.
-
Ensures Compliance with Regulations
Many buildings must comply with safety, fire and environmental regulations. CMMS stores maintenance records and keeps inspections on schedule to avoid legal risks.
👉 Example: An office complex must perform regular fire alarm and sprinkler inspections. CMMS sends automated reminders, ensuring compliance and reducing liability.
-
Enhances Productivity for Maintenance Teams
CMMS eliminates paperwork and inefficiencies, helping maintenance staff prioritize and complete tasks faster.
👉 Example: A university campus has hundreds of classrooms, restrooms and dormitories. A CMMS helps staff prioritize urgent issues, such as plumbing leaks, while keeping track of routine maintenance.
Key Features of a CMMS for Building Maintenance
When choosing a CMMS for facility management, look for these essential features:
✅ Work Order Management
- Create, assign and track maintenance requests
- Set priority levels for urgent repairs
- Allow staff to update work orders from mobile devices
✅ Preventative Maintenance Scheduling
- Automate routine maintenance (e.g., HVAC servicing, plumbing checks)
- Receive alerts when maintenance is due
- Reduce unexpected breakdowns
✅ Asset Management
- Track building systems and equipment (HVAC, elevators, lighting)
- Store equipment manuals and service history
- Monitor asset performance and lifespan
✅ Inventory & Spare Parts Management
- Keep track of parts needed for repairs
- Avoid stock shortages for critical supplies
- Automate reordering of commonly used items
✅ Compliance & Reporting
- Log maintenance records for audits
- Ensure adherence to safety and health regulations
- Generate reports on maintenance costs and efficiency
✅ Mobile Access for Technicians
- Allow field technicians to update work orders via smartphone/tablet
- Upload photos of repairs for documentation
- Reduce communication delays
Best Practices for Implementing CMMS in Building Maintenance
-
Get Buy-in from Your Team
Introduce CMMS as a tool that simplifies work, not extra bureaucracy. Show maintenance teams how it saves time and makes their jobs easier.
-
Start with a Small Pilot Project
Before rolling out CMMS across all buildings, test it in one facility to fine-tune processes.
-
Train Employees on CMMS Usage
Proper training ensures that all staff members can log work orders, track maintenance and access important data.
-
Integrate with Other Systems
If your business already uses property management software, choose a CMMS that integrates with existing tools.
-
Regularly Update Maintenance Data
Keep asset records, service logs and inventory lists up to date for accurate tracking and reporting.
-
Analyze CMMS Data for Continuous Improvement
Use reports and analytics to identify maintenance trends, cost savings and areas for improvement.
Real-World CMMS Success Stories
✅ Retail Stores – Large retail chains use CMMS to keep track of HVAC, refrigeration and lighting maintenance, reducing downtime and energy costs.
✅ Healthcare Facilities – Hospitals rely on CMMS to ensure medical equipment and building systems (like generators and air filtration) are always functional.
✅ Office Buildings – Property management firms use CMMS to handle tenant maintenance requests, improving response times and satisfaction.
✅ Manufacturing Plants – CMMS prevents equipment failures that could halt production and cause financial losses.
✅ Hotels & Resorts – CMMS helps keep guest rooms, pools and common areas in top condition, ensuring positive customer experiences.
CMMS is a Must-Have for Building Maintenance
A CMMS is not just a “nice-to-have” tool—it’s a necessity for any business that manages buildings and facilities.
By automating work orders, tracking maintenance schedules and preventing costly repairs, CMMS transforms how buildings are maintained, saving time, money and effort.
If you want a smoother, more efficient maintenance operation, investing in a CMMS is the smartest move you can make.
Image by teksomolika on Freepik.
Related posts
Here are some resources to help you get more out of your assets

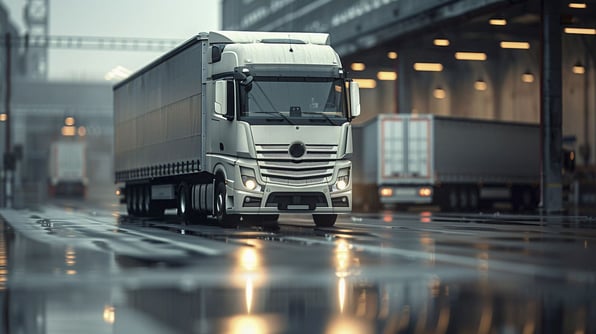
Ciprian Chiripuci
Truck Sealing in Delivery Logistics: Definition, Benefits and Best Practices
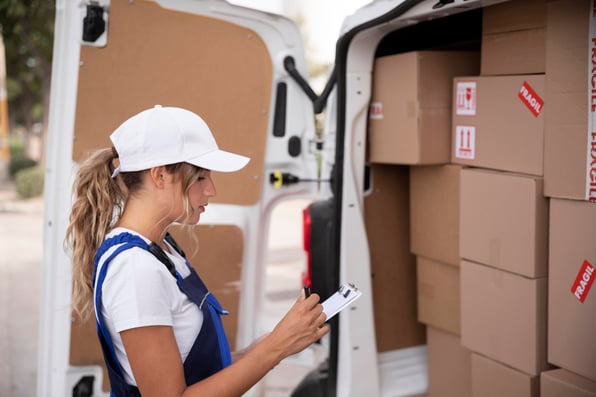
Ciprian Chiripuci
Mastering that Last Mile
READY TO TALK?